Forschung // Additive Fertigung (3D-Druck)
SmartPro – Key to Smart Products!
Additive Fertigung – oft besser bekannt als 3D-Druck – ist eine mächtige Technologie, um Ressourcen zu schonen.
Der Verbrauch wird limitiert, indem Material effizient nur an den Stellen eingesetzt wird, an denen es funktional auch benötigt wird. Neue additive Technologien, Materialien und Konzepte werden in den SmartPro-Impulsprojekten AddFunk (2017-2021) und Smart-ADD (2021-2025) im engen Austausch mit den SmartPro-Anwendungsfeldern (Energiewandler, Energiespeicher und Leichtbau) querschnittlich entwickelt.
Die SmartPro-Impulsprojekte im Bereich der Additiven Fertigung (3D-Druck)
Smart-ADD
// Projektlaufzeit: 01.06.2021 bis 31.05.2025
Projektleitung
Prof. Dr. Rainer Börret
Zentrum für Optische Technologien
Tel.: +49 (0)7361 576-3482
rainer.boerret@hs-aalen.de
Projektpartner
Hochschule Aalen
- Dr. Timo Bernthaler, Institut für Materialforschung
- Prof. Dr. Andreas Heinrich, Zentrum für Optische Technologien
- Prof. Dr. Gerhard Schneider, Institut für Materialforschung
- Prof. Dr. Harald Riegel, LaserApplikationsZentrum
- Prof. Dr. Markus Merkel, Zentrum für Virtuelle Produktentwicklung
- Prof. Dr. Anne Harth, Zentrum für Optische Technologien
Unternehmen
- BWF Profiles GmbH & Co. KG
- Carl Zeiss Jena GmbH / Standort Oberkochen
- Carl Zeiss SMT
- EMAG LaserTec GmbH
- Franke GmbH
- C. Starck GmbH
- HECKERWERKE GmbH
- MAPAL Dr. Kress KG
- MAYRHÖNES Metallumformung GmbH
- TRIES GmbH & Co. KG
Weitere Forschungsinstitutionen
- Glasgow Caledonian University (UK)
- Technische Universität München – Lehrstuhl für Werkstoffkunde und Werkstoffmechanik
Transferakteure
- Photonics BW e.V.
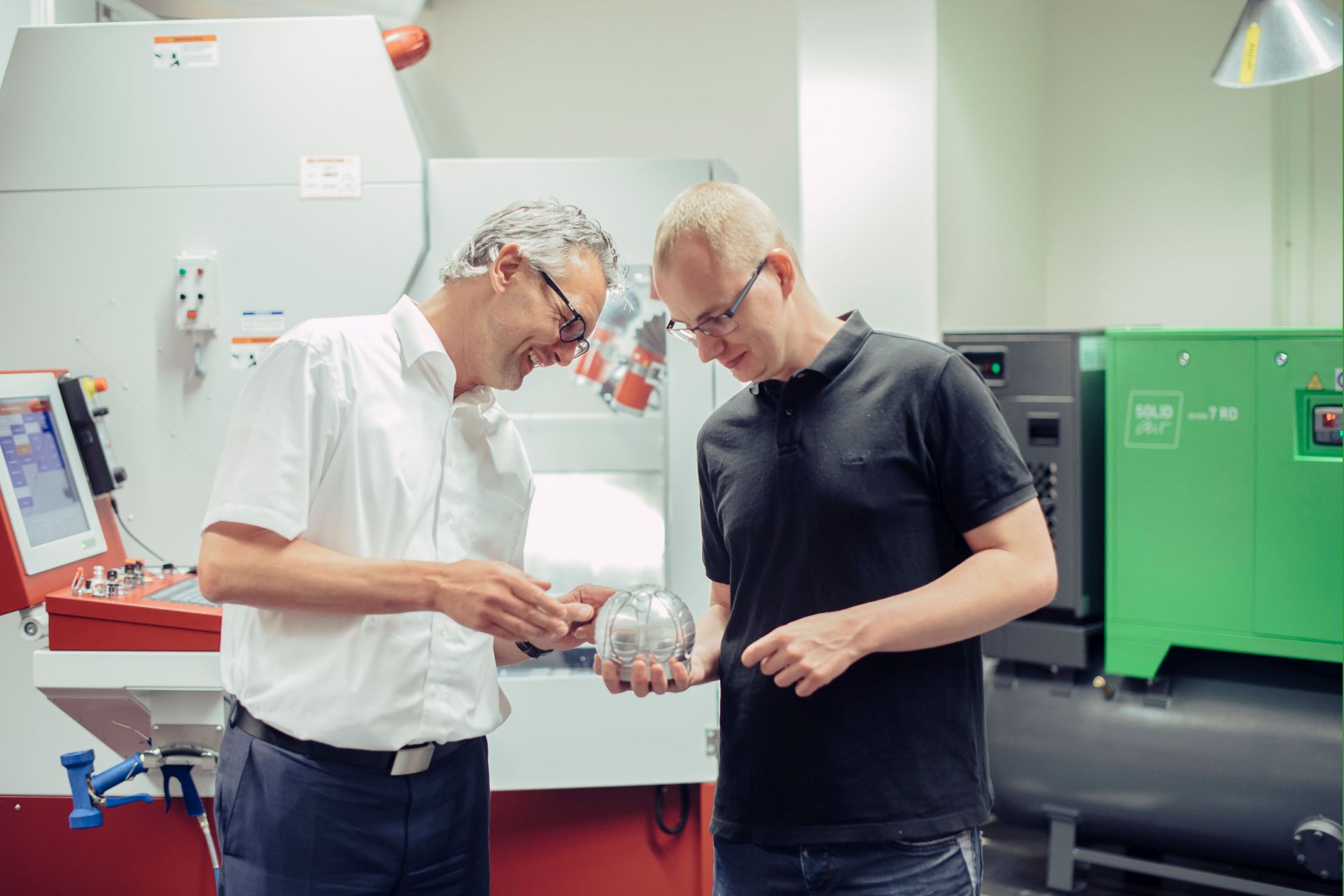
Plattform Additive Technologien für Ressourcen- und Energieeffizienz (Smart-ADD)
Im querschnittlich angelegten Impulsprojekt Smart-ADD wird eine Plattform für neue additive Technologien entwickelt, die an den Bedarfen der Forschungsinhalte in den SmartPro-Anwendungsfeldern ausgerichtet ist. Die Plattform unterstützt unterschiedlichste Anwendungen, indem sie die notwendige Hard- und Software sowie erforderliche Materialien und spezifisch angepasste Prozesse bereitstellt. So wird das Ziel verfolgt, nicht nur Linsen für LEDs oder Magnete für zukünftige Elektromotoren, sondern auch auf die Anforderungen zugeschnittene Leichtbaustrukturen und Cobalt-freie Hartmetalle für ressourcenschonende Werkzeuge mit geringem Verschleiß zu drucken.
Zu den Vorteilen der additiven Fertigung gehört es, dass Bauteile mit Geometrien hergestellt werden können, die mit herkömmlichen Methoden nicht zugänglich sind, und somit ganz neue, vor allem auch energieeffiziente, Konzepte realisierbar sind. Gleichzeitig lässt sich dabei sogar Material einsparen. Das reduziert nicht nur Kosten, sondern schont auch kritische Ressourcen, spart Energie und trägt somit seinen Teil zum Klimaschutz bei.
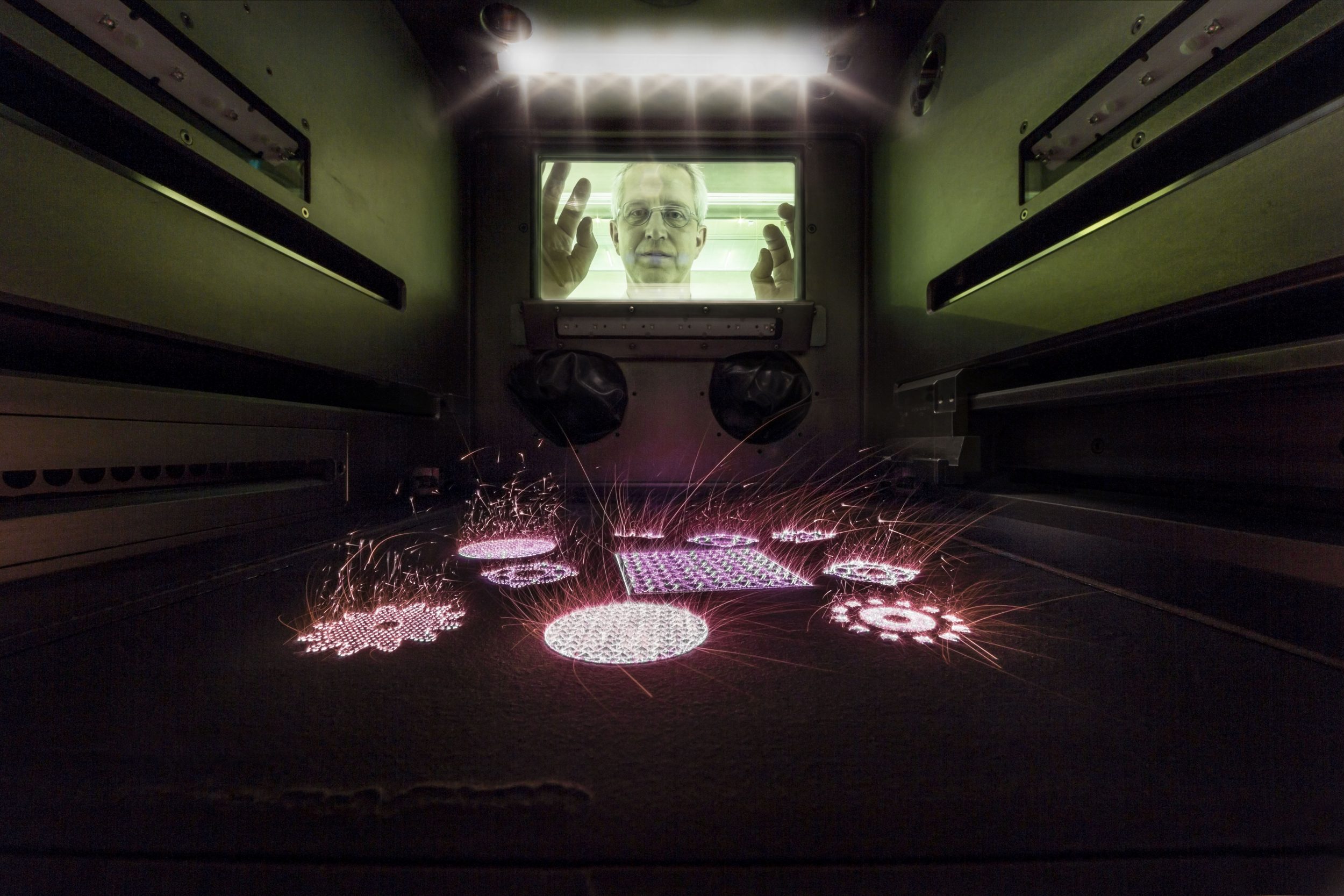
Additiv gefertigte funktionale und intelligente Komponenten (AddFunk)
Additive Fertigung ist eine der Schlüsseltechnologien für Industrie 4.0 und das Internet der Dinge. Sie ermöglicht die wirtschaftliche ressourceneffiziente Herstellung individualisierter Produkte. Diesbezügliche Fragestellungen der Industrie – vom lokalen KMU in der Kunststoffverarbeitung oder Werkzeugherstellung bis hin zu internationalen Großkonzernen im Bereich Maschinenbau und Optik – griff das Impulsprojekt AddFunK auf und bearbeitete diese umfassend.
Dabei wurde die additive Fertigung in Richtung innovativer integrierter Komponentenlösungen für energieeffiziente Produkte weiterentwickelt. Die entwickelten 3D-Druckprozesse umfassen einerseits Leichtbauwerkstoffe, verschleißbeständige hartmetallische Werkstoffe oder neue Materialkombinationen (zum Beispiel Verbundwerkstoffen aus keramischen Materialien in einer metallischen Matrix, CerMets). Andererseits wurden optischen Kunststoffe zur Herstellung intelligenter Sensoren in cyberphysischen Systemen erschlossen, die beispielsweise in industriellen Produktionsanlagen zum Einsatz kommen. Neben neuen Anwendungsmöglichkeiten und der Funktionsintegration durch intelligente Fertigungsprozesse in den Bereichen Metall und optische Elemente standen die konstruktive Gestaltung der Komponenten sowie die Einstellung gewünschter physikalischer Eigenschaften im Fokus. Wichtige Aspekte waren dabei auch die Qualität der Oberfläche der Bauteile und deren Mikrostrukturierung durch Laserbearbeitung.
AddFunk
// Projektlaufzeit: 01.0.2017 bis 31.08.2021
Projektleitung
Prof. Dr. Rainer Börret
Zentrum für Optische Technologien
Tel.: +49 (0)7361 576-3482
rainer.boerret@hs-aalen.de
Projektpartner
Hochschule Aalen
- Dr. Timo Bernthaler, Institut für Materialforschung
- Prof. Dr. Andreas Heinrich, Zentrum für Optische Technologien
- Prof. Dr. Gerhard Schneider, Institut für Materialforschung
- Prof. Dr. Harald Riegel, LaserApplikationsZentrum
- Prof. Dr. Markus Merkel, Zentrum für Virtuelle Produktentwicklung
Unternehmen
- BWF Profiles GmbH & Co. KG
- Carl Zeiss Jena GmbH
- Carl Zeiss Vision GmbH
- Eluminocity GmbH
- Franke GmbH
- HECKERWERKE GmbH
- MAPAL Dr. Kress KG
- Oppold System International GmbH
- TRUMPF Laser- und Systemtechnik GmbH
- F. & G. Hachtel GmbH & Co. KG
Weitere Forschungsinstitutionen
- Glasgow Caledonian University
- Karlsruher Institut für Technologie – Institut für Angewandte Materialien, keramische Werkstoffe und Technologien (IAM-KWT)
- Universität Ulm
Transferakteure
- Photonics BW e. V.
Folgen Sie uns!
Immer auf dem Laufenden
über das SmartPro-Netzwerk bleiben Sie
auch auf LinkedIn.
Klicken Sie doch mal vorbei!
Explorative Projekte
Die vielfältigen Einsatzmöglichkeiten von additiver Fertigung wurden in den fünf explorativen Projekten voll ausgespielt. So wurden in den Projekten ProxiMat und HEROD innovative Einsatzmöglichkeiten für additive Fertigung in den SmartPro-Anwendungsfeldern Energiewandler und Leichtbau erforscht, während die Anwendung von Machine Learning – Methoden für die Weiterentwicklung von 3D-Druckprozessen in DiMa untersucht wurde. Durch das Projekt 3DPräkomMed wurde der Anwendungsbereich additiver Fertigung sogar nochmals erweitert – für hochpräzise Anwendungen wie intelligente Hörgeräte-Komponenten oder Bauteile für die Luft- und Raumfahrtindustrie. Durch die Kooperation Forschender aus unterschiedlichen Schwerpunkten wurden die Anwendungsfelder noch enger miteinander verknüpft.
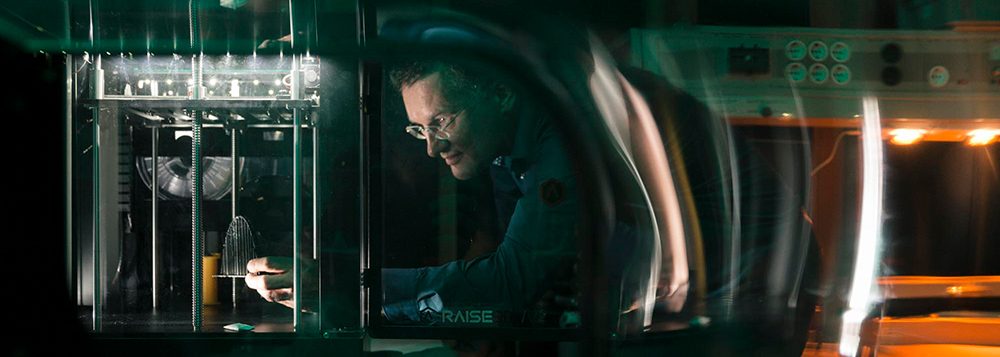
3DGRIN // 3D-Druck von Gradientenindexoptiken
01.07.2018 – 30.09.2019
Konventionelle optische Bauelemente bestehen aus einem Material mit homogenen optischen Eigenschaften wie z.B. dem Brechungsindex. Ziel des Projekts 3DGRIN war die Entwicklung einer Gradientenindexoptik (GRIN-Optik), bei der Materialien mit unterschiedlichen Brechungsindices kombiniert werden.
Gradientenindexoptiken generieren neue Eigenschaften optischer Bauteile und versprechen damit innovative Anwendungen, wie sie für hochintegrierte Systeme notwendig sind, z.B. für Augmented Reality - Systeme. Bisher konnten sie nur mit hohem Aufwand und hohen Kosten sowie für eingeschränkte Funktionalitäten gefertigt werden. Im Vorhaben 3DGRIN wurde daher die innovative und wirtschaftliche Fertigung von Gradientenindexoptiken in einem einzigen Fertigungsprozess mittels 3D-Druck untersucht.
3DGRIN unterstützte durch erfolgreiche Verwertung der Projektergebnisse durch SmartPro-Unternehmenspartner und gemeinsame Anschlussprojekte auch besonders die Erreichung der strategischen Ziele der SmartPro-Partnerschaft.
- Projektleitung
Prof. Dr. Andreas Heinrich, Zentrum für Optische Technologien
- Projektpartner
Prof. Dr. Harald Riegel, LaserApplikationsZentrum
Prof. Dr. Rainer Börret, Zentrum für Optische Technologien
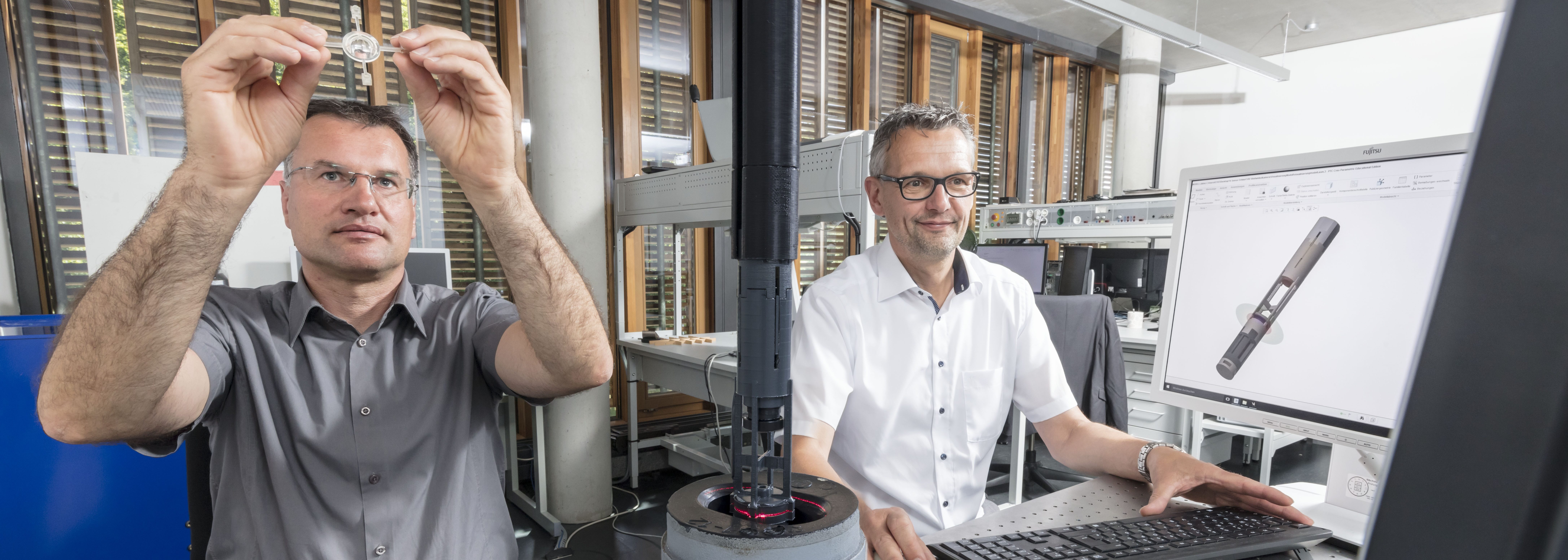
HEROD // Simulation des 3D-Drucks hochpräziser Kunststoffteile
01.01.2019 – 31.05.2020
Ziel des Projekts HEROD war die Entwicklung eines Simulationsmodells für den 3D-Kunststoffdruck.
3D-gedruckte Kunststoffbauteile werden schichtweise im Drucker aufgebaut. Die Verbindung der Schichten während des Druckprozesses ist eine Schwachstelle. Die mechanischen Eigenschaften des gesamten Bauteils hängen stark davon ab, wie gut sie sich ausbildet.
Mit dem in HEROD entwickelten Simulationsmodell wurden Fortschritte auf dem Weg zur Vorhersage der mechanischen Eigenschaften der Komponenten erzielt. Das Modell beruht auf Einzelelementen, die einzelnen 3D-gedruckten Tropfen entsprechen, und wurde experimentell durch Festigkeitstests überprüft. Mit dem Modell lässt sich ermitteln, ob mittels 3D-Druck Kunststoffteile hergestellt werden können, die ähnliche mechanische Eigenschaften und identische Belastbarkeit wie die derzeit in der Industrie verwendeten Spritzgussteile aufweisen. Dies ebnet den Weg dahin, z.B. Ersatzteile aus Kunststoff in kleinen Stückzahlen schnell, einfach und hochpräzise mittels 3D-Druck fertigen zu können.
- Projektleitung
Prof. Dr. Rainer Börret, Zentrum für Optische Technologien
- Projektpartner
Dr. Wolfgang Rimkus, Technologiezentrum Leichtbau
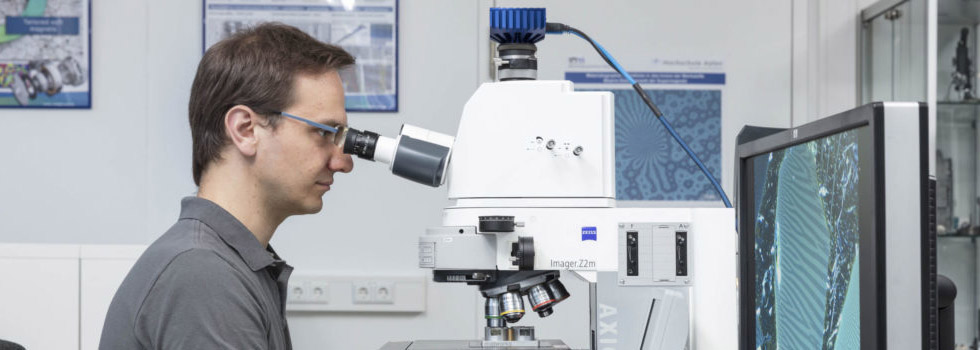
ProxiMat // Prozessinnovationen für Additive Fertigung oxidationsempfindlicher Materialien
01.08.2020 bis 31.10.2021
Die Entwicklung kosteneffizienter und ressourcenschonender Dauermagnete ist eine der Grundlagen für innovative Energiewandler für die Elektromobilität der Zukunft. Der Einsatz neuer Fertigungstechnologien wie die der Additiven Fertigung (z. B. 3D-Druck) eröffnen innovative Ansätze für die Produktion energie- und ressourceneffizienter Energiewandler für eine Vielzahl von Anwendungsgebieten. In dem Explorativen Projekt ProxiMat stand die Nutzung dieser Technologie zur Verbesserung der Eigenschaften von Dauermagneten im Mittelpunkt.
In einem innovativen Ansatz wurden im Labormaßstab optimierte, kleinstmögliche Korngrößen von additiv gefertigten Neodym-Eisen-Bor- Magneten mit ultrafeiner gerichteter Gefügestruktur experimentell ermittelt. In direktem Zusammenhang hiermit wurden auch alternative und wirtschaftlichere Verfahren zur Herstellung der verwendeten Ausgangslegierungen untersucht.
Ein weiterer Fokus in ProxiMat war die Erprobung eines Einsatzes der laserbasierten additiven Fertigung von Dauermagnetkomponenten aus Carbon-Eisen-Neodym, wie es zurzeit für gussgefertigte Elemente bereits möglich ist. Ebenso wurden die sich eröffnenden Möglichkeiten der Fertigungstechnik zur Herstellung von anisotropen Komponenten untersucht.
- Projektleitung
Prof. Dr. Dagmar Goll, Institut für Materialforschung Aalen
Dr. Timo Bernthaler, Institut für Materialforschung
Prof. Dr. Gerhard Schneider, Institut für Materialforschung
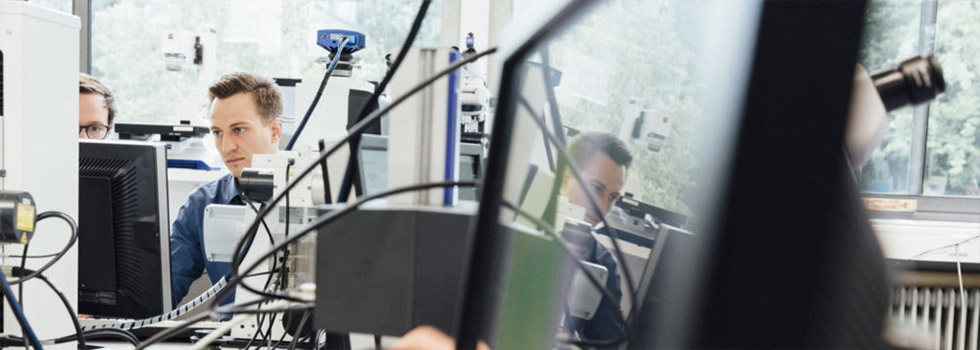
DiMa // Digitalisierungspotenziale der Materialforschung in SmartPro
01.10.2019 – 30.09.2020
Das Explorative Projekt DiMa besteht aus verschiedenen Teilprojekten, deren methodischer Ansatz auf die jeweiligen Forschungsschwerpunkte der Impulsprojekte inhaltlich angepasst ist.
Im Projekt werden die Expertisen von Data Science Experten sowie aus den anderen Forschungsbereichen von SmartPro zusammengeführt und somit in interdisziplinären Ansätzen neue Forschungsinhalte generiert.
Die Teilprojekte sind jeweils einem Impulsprojekt zugeordnet und dienen als Ausgangpunkt für die Entwicklung des querschnittlich angelegten neuen Impulsprojekts mit dem Schwerpunkt Data Sciences.
In SmartPrint (zugeordnet dem Impulsprojekt AddFunk) sollen die Prozessparameter und Materialeigenschaften der durch 3D Druck gefertigten optischen Komponenten hinsichtlich der resultierenden Teilequalität mit Hilfe von Machine Learning untersucht werden.
- Projektleitung
Prof. Dr. Ricardo Büttner, Wirtschaftsinformatik
- Projektpartner
Prof. Dr. Manfred Rössle, Wirtschaftsinformatik
Prof. Dr. Andreas Heinrich, Zentrum für Optische Technologien
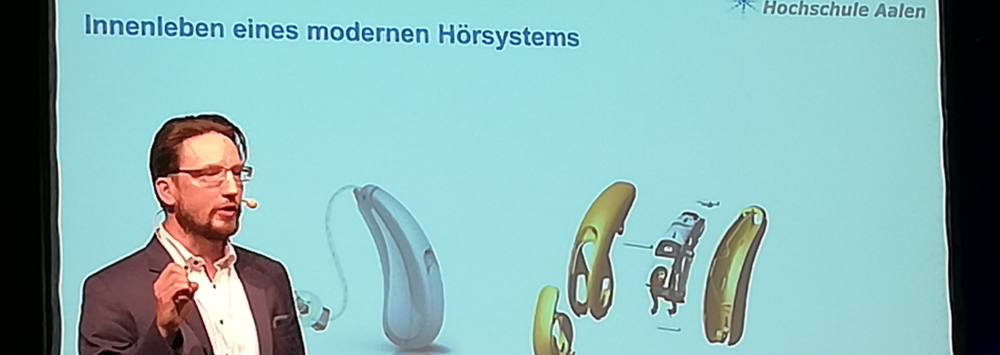
3DPräkomMed // 3D-Druck für Hochpräzisionskomponenten und Medizingerätetechnik: neue Anwendungsgebiete durch smarte Materialien und intelligentes Design
01.05.2019 – 30.04.2020
Die additive Fertigung zur Herstellung von komplex geformten und individualisierten Komponenten wird in der Zukunft in vielen Bereichen völlig neue Produkte mit optimierten physikalischen Eigenschaften ermöglichen. Im Vorhaben 3DPräkomMed wurden in zwei Teilprojekten einerseits die Nutzung thermostabiler Legierungen untersucht und andererseits Otoplastiken entwickelt, deren Gehörschutzfunktion durch einen Impulsschallfilter funktional erweitert werden kann.
Das Teilprojekt „Additive Fertigung von thermisch beanspruchten Komponenten für Hochpräzisionsanwendungen“ (AtheK) hat die Verwendungsmöglichkeiten spezifischer Legierungen in der additiven Fertigung untersucht. Im Mittelpunkt standen Legierungen, die im makroskopischen Bereich thermisch stabil sind. Die Nutzung solcher Materialien ist von besonderer Bedeutung. Denn besonders für zunehmend eingesetzte Hochpräzisionsanwendungen ist es entscheidend, dass die Bauteile auch unter Nutzung und dadurch bedingte Erwärmung und Ausdehnung formstabil bleiben. Nur Materialien mit sehr geringen Ausdehnungskoeffizienten erlauben daher die Fertigung durchgängig passgenauer Komponenten, die auch bei verschiedenen Temperaturen formstabil bleiben.
Im Teilprojekt „3D Otoplastikdruck“ (SmartVent) wurden additiv gefertigte individualisierte Otoplastiken (Hörgerätekomponenten) hinsichtlich ihrer akustischen Eigenschaften verbessert. Im Wesentlichen wurden Modifikationen durchgeführt, die schallfilternd wirken und verhindern, dass impulsartiger Schall durch die Belüftungsbohrungen gelangt. Ziel war zunächst die Entwicklung eines manuell steuerbaren Filters.
- Projektleitung
Prof. Dr. Markus Merkel, Zentrum für Virtuelle Produktentwicklung
- Projektpartner
Dr. Timo Bernthaler, Institut für Materialforschung Aalen
Prof. Dr. Steffen Kreikemeier, Gesundheitstechnologie
KMU-Projekt
PROFM // 01.05.2019 bis 30.04.2020
Prozessbedingte Formgenauigkeit smarter 3D-Druck-Materialien
Die Anwendung von 3D-Druckverfahren in der Fertigung ist aufgrund der hohen Flexibilität und Präzision eine Methode, die in vielen Bereichen eingesetzt werden kann. Geringe Stückzahlen und hochpräzise Produktabmessungen ohne die Notwendigkeit weiterer Investitionen sind hier von großer Bedeutung für die Akzeptanz in den Unternehmen. Die Vorteile können in der Industrie erst dann voll genutzt werden, wenn die Herstellung 3D-gedruckter Bauteile gelingt, welche die gewünschten Eigenschaften aufweisen. Dies ist zurzeit in vielen Bereichen noch eine große Herausforderung.
Ziel des KMU-Projekts PROFM war die Produktion additiv gefertigter Bauteile, die konventionell hergestellten Produkten gleichwertig sind und ähnliche zentrale physikalische Eigenschaften aufweisen. Da es sich gezeigt hat, dass der Einsatz konventionell verwendeter Materialen nicht zu hinreichend guten Ergebnissen führt, wurden alternative Materialien getestet. Eine spezifische Optimierung der Prozessparameter war hierbei von besonderer Bedeutung und bietet nun die Möglichkeit der gezielten Adaption an die jeweilige Anwendung.
- Projektleitung
F. & G. Hachtel GmbH & Co. KG - Projektpartner (Unternehmen)
Prof. Dr. Rainer Börret, Zentrum für Optische Technologien
Verwandte Projekte
Die Arbeitsgruppen des SmartPro-Netzwerks an der Hochschule Aalen führen neben den SmartPro-Projekten zahlreiche weitere Forschungsvorhaben durch. Darin werden oft verwandte Fragestellungen verfolgt, die thematischen oder methodischen Bezug zu SmartPro aufweisen.
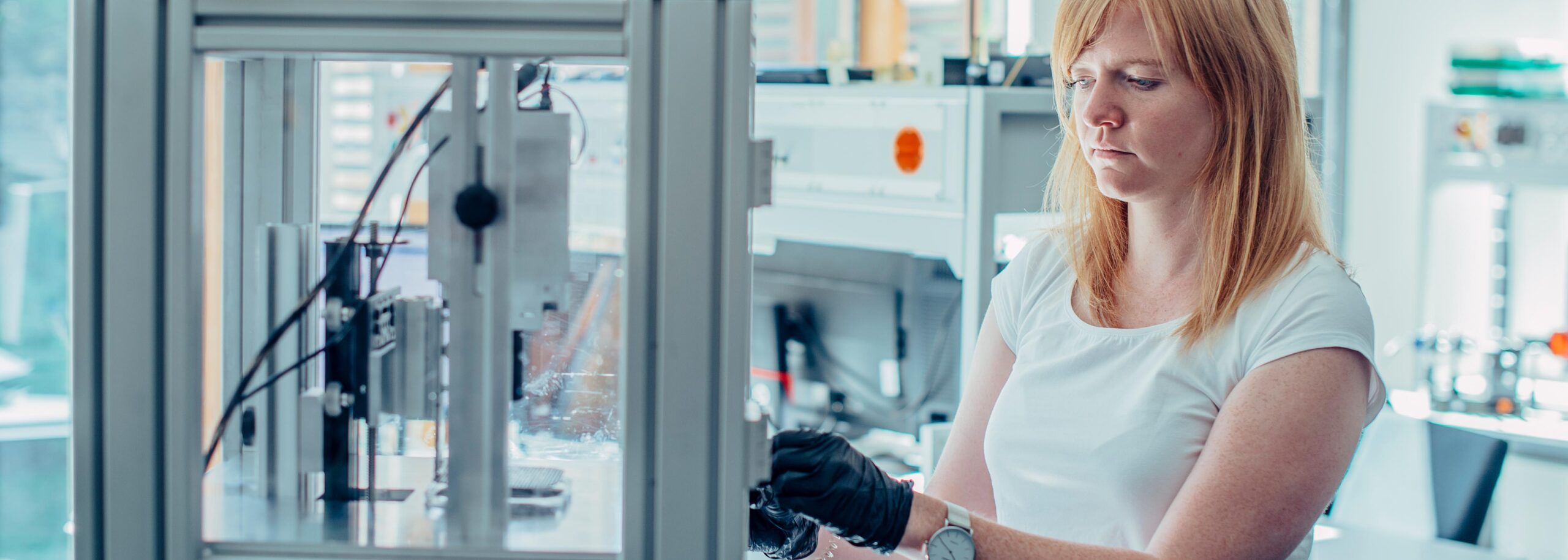
InProGrin // Additiv gefertigte Gradienten-Index-Optiken: Verteilung des 3D-Brechungsindexes
01.07.2024 – 30.06.2027
Im Projekt InProGrin wird ein neues, additives Fertigungsverfahren zur Herstellung von Gradienten-Index (GRIN) – Optiken erforscht, die beispielsweise oft in Mess- und Sensorsystemen eingesetzt werden. Untersucht werden die optischen Eigenschaften der Bauteile und die Einflüsse des additiven Fertigungsprozesses auf diese. Darauf basierend ist zur Qualitätssicherung eine schnelle und robuste In-Prozess-Messtechnik zu entwickeln.
Die additive Fertigung gewinnt in der Herstellung komplexer optischer Komponenten zunehmend an Bedeutung. Für die Fertigung von Einzelstücken oder geringer Stückzahlen sind die Prozesse gut aufgestellt. Für den Einsatz in der Massenproduktion hingegen fehlen präzise und hochflexible Verfahren zur prozessbegleitenden Qualitätssicherung und Bewertung der optischen Eigenschaften der Bauteile während des Fertigungsprozesses.
Dies gilt insbesondere für GRIN-Optiken, in denen der Brechungsindex einen Gradienten aufweist, und die beispielsweise in vielen präzisen Mess- und Sensorsystemen, Endoskopen, aber auch allgemein in optischen Abbildungssystemen eingesetzt werden. Ihr Vorteil liegt vor allem in einer in das Volumen integrierten Funktionalität, ihrer Miniaturisierung und in planen Oberflächen – im Gegensatz zu gekrümmten Oberflächen bei Linsen. Konventionell werden sie z.B. über Ionenaustauschverfahren oder chemische Beschichtungsprozesse hergestellt. Neue Ansätze nutzen die Vorteile additiver Fertigung wie Designfreiheit und Ressourcenschonung. Doch welche Qualität weisen additiv gefertigte GRIN-Optiken auf? Wie werden die Verteilung des Brechungsindexes und die optischen Eigenschaften durch den additiven Fertigungsprozess beeinflusst? Was passiert bei Prozessabweichungen?
Im Projekt InProGrin werden diese Zusammenhänge und damit die Grundlagen für eine prozessbegleitende Qualitätssicherung erforscht. Ein umfassendes Verständnis ermöglichte die Auslegung einer geeigneten Messtechnik und die Kompensation von Abweichungen während des Fertigungsprozesses. Mit den Partnern an der Universität Bremen setzen die Forschenden dabei auf eine mathematisch-physikalische Modellierung und die Entwicklung eines Algorithmus, um Fertigungsabweichungen zu kompensieren und den Prozess zu optimieren. Die In-Line-Messtechnik zur Qualitätssicherung wird auf Basis einer lagenweisen Wellenfrontmessung entwickelt werden. Die Integration bildet eine Grundlage zur aktiven Regelung des additiven Fertigungsprozesses.
Weitere Informationen
- zum Projekt „InProGrin – In-Situ-Erfassung der 3D-Brechungsindexverteilung in der additiven Fertigung von GRIN-Optiken: GEPRIS-Projektdatenbank der DFG
- zum explorativen SmartPro-Projekt 3DGRIN, in dem Prof. Dr. Andreas Heinrich erste Ansätze zur additiven Fertigung von GRIN-Optiken untersucht hat
Projektleitung
Prof. Dr. Andreas Heinrich, Zentrum für Optische Technologien
Projektpartner
Universität Bremen
BIAS – Bremener Institut für angewandte Strahltechnik GmbH
Förderung
Das Projekt wird von der Deutschen Forschungsgemeinschaft – DFG im Rahmen einer Sachbeihilfe gefördert. Rund 350.000 Euro gehen an die Hochschule Aalen.
Foto: Nachwuchswissenschaftlerin am Zentrum für Optische Technoligien der Hochschule Aalen. © Hochschule Aalen
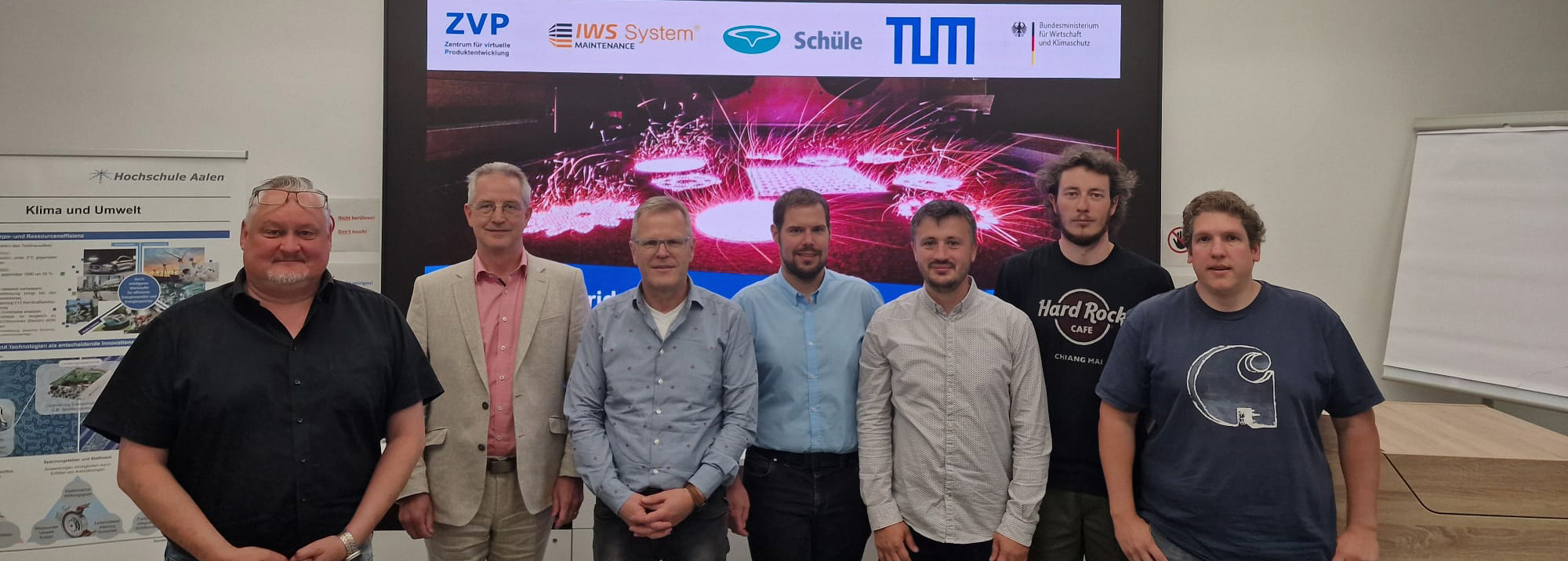
Hybrid-3D // Ressourceneffizienter hybrider Produktionsprozess aus additiver Fertigung und Kokillenguss
01.05.2024 – 31.10.2026
Ziel des Projektes Hybrid-3D ist die Entwicklung eines hybriden Fertigungsprozesses, der die Vorzüge mehrerer Fertigungsprozesse vereint und gleichzeitig einen ressourcenschonenden Materialeinsatz ermöglicht, für ein Hallenkran-Fahrwerk. Hierfür wird zunächst ein Hallenkran-Fahrwerk eines Leichtlauf-Kransystems in seinen Anforderungen definiert und anschließend konstruktiv für den hybriden Fertigungsprozess optimiert. Dieser kombiniert die Vorteile der additiven Fertigung mit dem klassischen Metallguss und bietet daher flexiblere Möglichkeiten der Konstruktion.
Das Hallenkran-Fahrwerk wird in einer bionischen Leichtbauvariante gefertigt, bei der eine hochfeste, verschleißbeständige additiv hergestellte Hülle mit einem kostengünstigen Kern aus recyceltem Aluminium ausgegossen wird. Im Vergleich zur bisherigen Schmiede-Konstruktion reduziert diese Bauweise die Anzahl der Fügeverbindungen, während die robuste äußere Hülle die Einsatzdauer verlängert und das geringere Gewicht das Ansprechverhalten des Kransystems verbessert. Gleichzeitig werden die mechanischen Eigenschaften des Gesamtsystems optimiert, unter anderem durch die Reduktion von Spannungen in den gefertigten Bauteilen.
Der innovative Ansatz im Teilprojekt der Hochschule Aalen ist die Entwicklung eines ressourcen- und energieeffizienten additiven Fertigungsprozesses unter Berücksichtigung der Einbindung einer Metallschmelze. Hier wird ausschlaggebend sein, wie dünnwandig die Außenhülle des Hallenkran-Fahrwerks realisiert werden soll. Entsprechend sind prozesstechnische Anpassungen notwendig, um die Qualitätsanforderungen einhalten zu können.
Ein weiterer innovativer Entwicklungsschritt ist die Integration eines Wärmebehandlungsprozesses in den Fertigungsbauraum des additiven Fertigungssystems. Dabei muss der additive Prozess auf die Wandstärke des Hallenkran-Fahrwerks angepasst werden. Diese Weiterentwicklung beinhaltet auch innovative Modifikationen des pulverbettbasierten Laser-Strahlschmelzens (englisch: Powder Bed Fusion – Laser Beam: PBF-LB) am PBF-LB-Fertigungssystem, um den Bauraum und bauraumnahe Bauteile für den Wärmeeinfluss einzustellen beziehungsweise davor zu schützen.
Projektleitung und Ansprechpartner an der Hochschule Aalen
Prof. Dr. Markus Merkel, Zentrum für Virtuelle Produktentwicklung
Dr.-Ing. Enes Sert, Zentrum für Virtuelle Produktentwicklung
Projektpartner
TU München (TUM)
IWS SYSTEM GmbH
Metallgießerei Schüle GmbH
Förderung
Das Projekt mit vollständigem Titel „Entwicklung eines Hallenkran-Fahrwerks für einen hybriden und ressourceneffizienten Herstellungsprozesses mittels additiver Fertigung und Kokillenguss und hybridem Materialeinsatz“ wird im Rahmen des Zentralen Innovationsprogramms Mittelstand (ZIM) durch das Bundesministerium für Wirtschaft und Klimaschutz mit 220.000 Euro gefördert.
Foto: Konsortium des Projekts Hybrid-3D bei einem Treffen an der Hochschule Aalen (HSAA): (v.l.) Heiko Petzoldt (Geschäftsführer IWS SYSTEM GmbH); Prof. Dr.-Ing. Markus Merkel (HSAA); Matthias Schüle (Geschäftsführer Metallgießerei Schüle GmbH); Dr. Leonhard Hitzler (TUM); Dr.-Ing. Enes Sert (HSAA); Lukas Apfelbacher (TUM); Christopher Rockinger (HSAA). © Hochschule Aalen
SmartPro // FH-Impuls:
Starke Fachhochschulen – Impuls für die Region
Die Hochschule Aalen hat sich mit SmartPro bundesweit in der Spitzengruppe der Fachhochschulen positioniert. Sie wird als eine von zehn Hochschulen in der Fördermaßnahme FH-Impuls des Bundesministeriums für Forschung, Technologie und Raumfahrt mit rund 10 Millionen Euro für gut acht Jahre bis 2025 gefördert. Kernziele sind der nachhaltige Ausbau des regionalen Transfer- und Kooperationsnetzwerks, die Stärkung der Forschung und Innovationskraft. SmartPro leistet Beiträge zu gesellschaftlichen Herausforderungen wie Klimaschutz, Mobilität und Digitalisierung.