Research // Additive Manufacturing (3D Printing)
SmartPro – Key to Smart Products!
Additive manufacturing − often better known as 3D printing − is a powerful technology that saves resources.
Resource consumption is limited by efficiently using material only where it is functionally needed. New additive technologies and materials as well as concepts are developed cross-sectionally in close collaboration with the SmartPro application fields (energy converters, energy storage systems, and lightweight construction). While the impulse project AddFunk (2017-2021) established at profound basis in SmartPro’s initiation phase, the impulse project Smart-ADD (2021-2025) of the intensification phase aims to consolidate and expand an additive manufacturing platform that offers numerous methodical approaches as well as new equipment and materials.
Smart-ADD
// Project duration: 01.06.2021 to 31.05.2025
Project management
Prof. Dr. Rainer Börret
Zentrum für Optische Technologien
Phone: +49 (0)7361 576-3482
rainer.boerret@hs-aalen.de
Project partner
Aalen University of Applied Sciences
- Dr. Timo Bernthaler, Materials Research Institute Aalen
- Prof. Dr. Andreas Heinrich, Center for Optical Technologies
- Prof. Dr. Gerhard Schneider, Materials Research Institute Aalen
- Prof. Dr. Harald Riegel, LaserApplicationCenter
- Prof. Dr. Markus Merkel, Zentrum für Virtuelle Produktentwicklung
- Prof. Dr. Anne Harth, Center for Optical Technologies
Companies
- BWF Profiles GmbH & Co. KG
- Carl Zeiss Jena GmbH / Standort Oberkochen
- Carl Zeiss SMT
- EMAG LaserTec GmbH
- Franke GmbH
- C. Starck GmbH
- HECKERWERKE GmbH
- MAPAL Dr. Kress KG
- MAYRHÖNES Metallumformung GmbH
- TRIES GmbH & Co. KG
Other research institutions
- Glasgow Caledonian University (UK)
- Technische Universität München – Lehrstuhl für Werkstoffkunde und Werkstoffmechanik
Transfer players
- Photonics BW e.V.
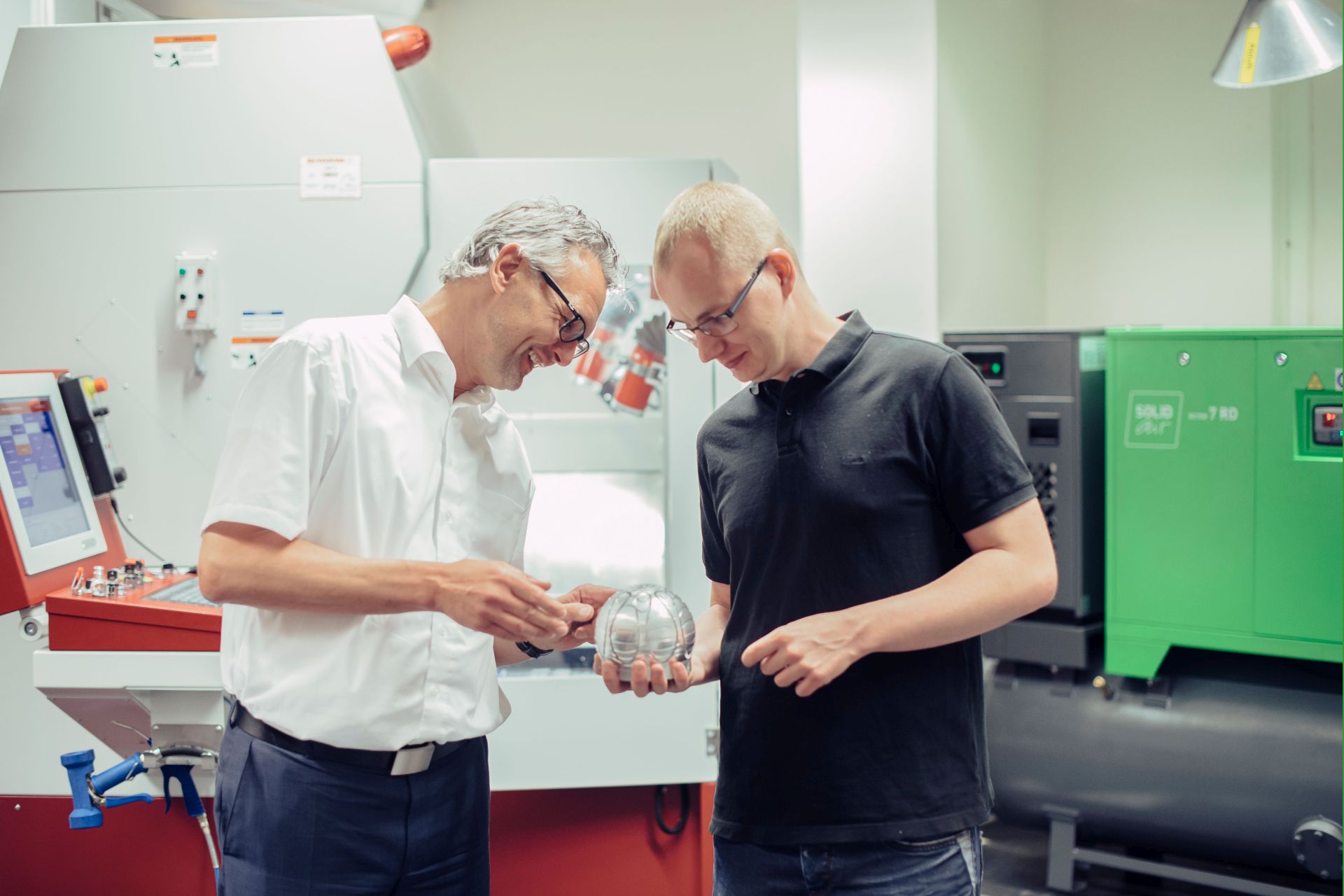
Smart-ADD
Platform for additive technologies for resource and energy efficiency
In the cross-sectional impulse project Smart-ADD, a platform for new additive technologies is developed that is aligned with the needs of the research topics in the SmartPro application fields. The platform will support a wide variety of applications by providing the necessary hardware and software as well as the required materials and specifically adapted processes. For example, the goal is to print not only lenses for LEDs (light-emitting diodes) or magnets for future electric motors, but also lightweight materials tailored to the particular requirements of the components or cobalt-free hard metals for resource-saving tools with low wear.
One of the remarkable advantages ofAadditive Manufacturing is the opportunity to produce components with geometries that are inaccessible using conventional production processes. Thus, additive approaches enable to realize completely new and above all resource-saving and energy-efficient concepts. This does not only reduce costs but also saves critical resources and energy needs – clearly, this is an important contribution to climate protection.
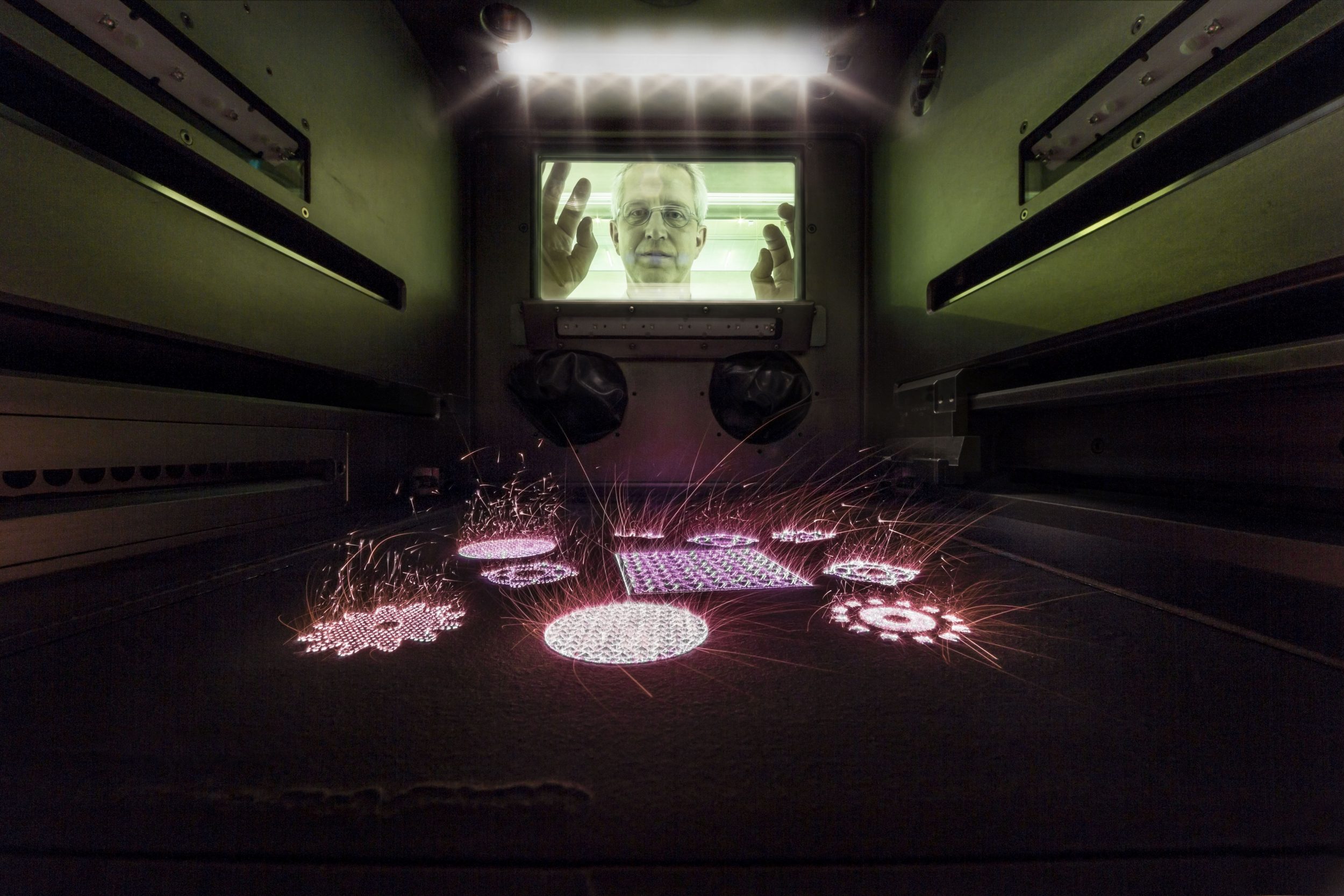
AddFunk
Additively Manufactured Functional and Smart Components
Additive manufacturing is one of the key technologies for Industry 4.0 and the Internet of Things (IoT). It paves the way for an economic resource-efficient production of individualized products. The impulse project AddFunK tackled questions from industry in these areas. Issues from local SMEs (small and medium-sized enterprises) in plastics processing or tool manufacturing to major international corporations in the fields of mechanical engineering or optics were comprehensively addressed.
Additive manufacturing was further developed towards innovative solutions to integrate new functions into components for energy-efficient products. The 3D printing processes developed include procedures for lightweight materials, wear-resistant hard metals, and new material combinations (for example composites of ceramic materials in a metallic matrix, CerMets). Additionally, optical synthetics were opened up for the production of intelligent sensors in cyber-physical systems, which are used for example in industrial production facilities. The achieved results highlighted new application possibilities and functional integration through intelligent manufacturing processes in the areas of metal and optical elements. Another focus was on the constructive design of these components and on the specific process and material configurations to fulfill the application-related requirements or to obtain new desired physical properties. Another important focus was on the quality of the surface of the printed components as well as their microstructuring by laser processing.
AddFunk
// Project duration: 01.06.2017 bis 31.05.2021
Project management
Prof. Dr. Rainer Börret
Zentrum für Optische Technologien
Phone: +49 (0)7361 576-3482
rainer.boerret@hs-aalen.de
Project partner
Aalen University
- Dr. Timo Bernthaler, Materials Research Institute Aalen
- Prof. Dr. Andreas Heinrich, Zentrum für Optische Technologien
- Prof. Dr. Gerhard Schneider, Materials Research Institute Aalen
- Prof. Dr. Harald Riegel, LaserApplikationsZentrum
- Prof. Dr. Markus Merkel, Zentrum für Virtuelle Produktentwicklung
Companies
- BWF Profiles GmbH & Co. KG
- Carl Zeiss Jena GmbH
- Carl Zeiss Vision GmbH
- Eluminocity GmbH
- Franke GmbH
- HECKERWERKE GmbH
- MAPAL Dr. Kress KG
- Oppold System International GmbH
- TRUMPF Laser- und Systemtechnik GmbH
- F. & G. Hachtel GmbH & Co. KG
Other research institutions
- Glasgow Caledonian University
- Karlsruher Institut für Technologie – Institut für Angewandte Materialien, keramische Werkstoffe und Technologien (IAM-KWT)
- Universität Ulm
Transfer players
- Photonics BW e. V.
Follow us!
Stay up to date about the
SmartPro network on LinkedIn!
Explorative projects
A wide range of potential applications for additive manufacturing (AM) also was exploited in five exploratory projects. While the projects ProxiMat and HEROD explored innovative AM approaches for energy converters or lightweight construction, respectively, the focus of DiMa was on the application of machine learning methods to improve the 3D printing processes for optical components. Through the project 3DPräkomMed, the scope of AM was even further expanded – for high-precision applications such as intelligent hearing aid components or parts for the aerospace industry. Benefitting from the cooperation of researchers from different disciplines, the SmartPro application fields were linked even more closely.
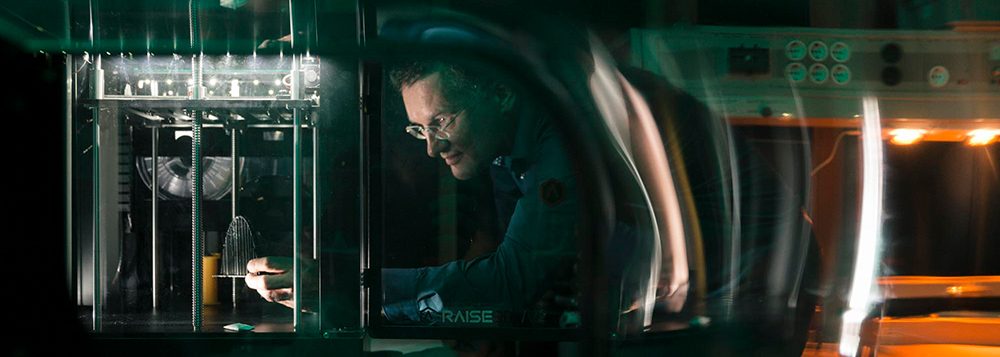
3DGRIN // 3D printing of gradient-index (GRIN) optics
01.07.2018 to 30.09.2019
Conventional optical devices consist of a material with homogeneous optical properties such as the refractive index. The goal of the project 3DGRIN was to develop graded-index (GRIN) optics combining materials with different refractive indices.
GRIN optics generate new properties of optical components and thus promise innovative applications as required for highly integrated systems, e.g. in the field of augmented reality. So far, their production had required great effort and high costs and allowed only limited functionalities. The results of 3DGRIN now enable an innovative and economically more attractive production of GRIN optics in a single manufacturing process by means of 3D printing.
3DGRIN also particularly supported the achievement of the strategic goals of the SmartPro partnership through successful utilization of the results by the industry partners. However, still there are a lot of methodolical challenges. To address open questions, joint follow-up projects have been started.
- Project management
Prof. Dr. Andreas Heinrich, Zentrum für Optische Technologien
- Project partner
Prof. Dr. Harald Riegel, LaserApplikationsZentrum
Prof. Dr. Rainer Börret, Zentrum für Optische Technologien
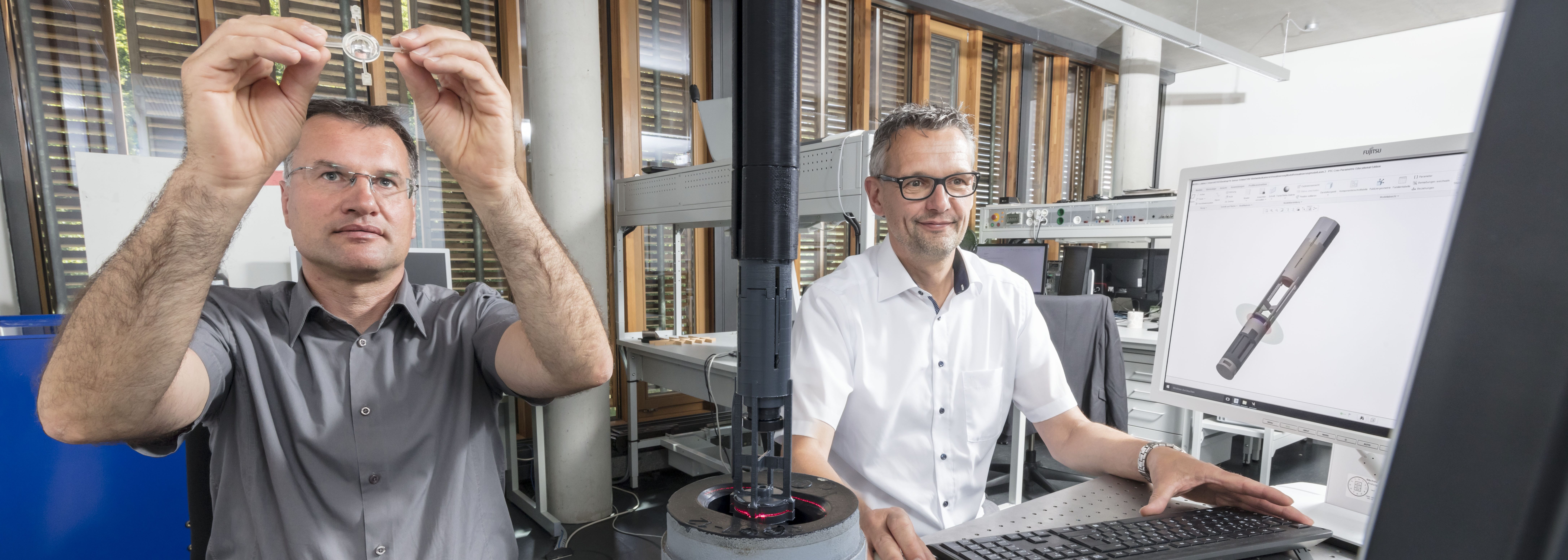
HEROD // Reproducibly manufactured high-strength plastic parts from the 3D printer using simulation
01.01.2019 to 31.05.2020
In the project HEROD, a simulation model for 3D printing of high-strength plastic parts was developed.
3D printed plastic components are built up layer by layer in the printer. The connection of the layers during the printing process is a weak point. The mechanical properties of the entire component depend heavily on how well it forms.
The simulation model developed in HEROD has made progress toward predicting the mechanical properties of the components. The model is based on single elements corresponding to individual 3D-printed drops and has been experimentally verified by strength tests. The model can be used to determine whether 3D printing can be used to produce plastic parts that have similar mechanical properties and identical load capacity to injection molded parts currently used in the industry. This paves the way to being able to produce, for example, spare parts made of plastic in small quantities quickly, easily, and with high precision using 3D printing.
- Project management
Prof. Dr. Rainer Börret, Zentrum für Optische Technologien
- Project partner
Dr. Wolfgang Rimkus, Technologiezentrum Leichtbau
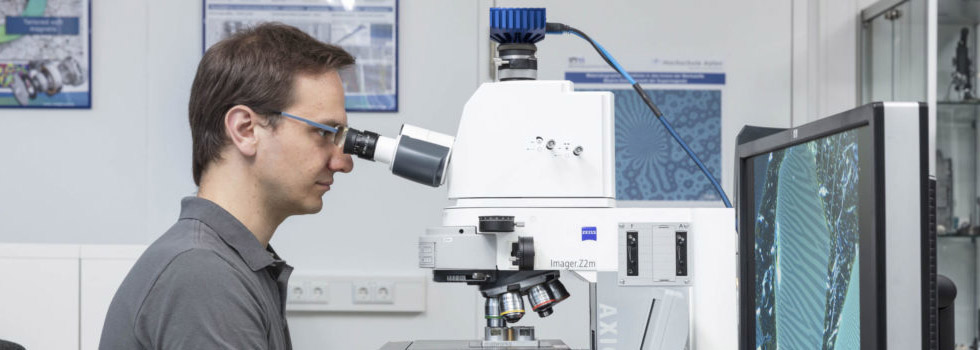
ProxiMat // Process innovations for additive manufacturing of oxidation-sensitive materials
01.08.2020 to 31.10.2021
The development of cost-effective and resource-saving permanent magnets is one of the foundations for innovative energy converters for future electromobility. The use of new manufacturing technologies such as additive manufacturing (for example 3D printing) opens up innovative approaches for the production of energy- and resource-efficient energy converters for a variety of application areas. The exploratory project ProxiMat focused on technological enhancements to improve the properties of permanent magnets.
In an innovative approach for Additive Manufacturing of neodymium-iron-boron magnets, optimized materials with the smallest possible grain size and ultra-fine directed microstructure were developed on a laboratory scale (and characteristic parameters experimentally determined). In direct connection with this, alternative and more economical processes for production the employed starting alloys were also investigated.
Beyond this, an application of laser-based additive manufacturing of permanent magnet components made of carbon-iron-neodymium was tested, as it is currently only available for cast elements. Likewise, the emerging possibilities of manufacturing technology for the production of anisotropic components were investigated.
- Project management
Prof. Dr. Dagmar Goll, Materials Research Institute Aalen
- Projektpartner
Dr. Timo Bernthaler, Materials Research Institute Aalen
Prof. Dr. Gerhard Schneider, Materials Research Institute Aalen
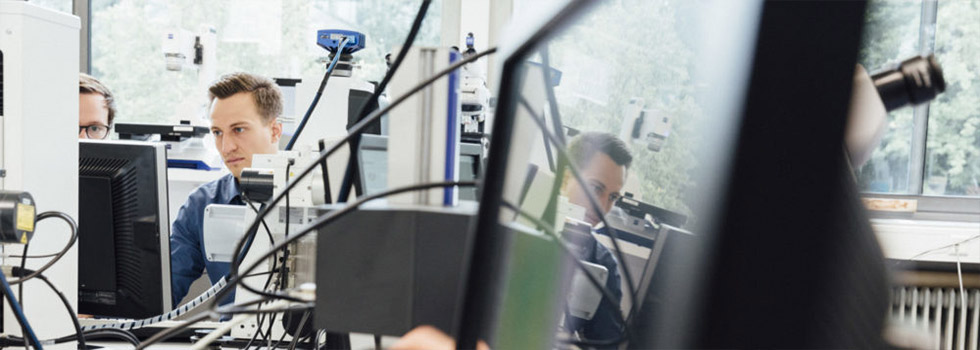
DiMa // Digitization potentials of materials research in SmartPro
01.10.2019 to 30.09.2020
In the explorative project DiMa, interdisciplinary approaches were used to generate new research content for the tailored further development of machine learning (ML) methods. For this, the methodological expertise of ML experts was combined with expertise in the other research areas of SmartPro.
Four subprojects were established, each assigned to one of the impulse projects, which served as a starting point for the development of the cross-sectional impulse project BEYOND with a focus on ML.
In SmartPrint (assigned to the impulse project AddFunk), the process parameters and material properties of optical components manufactured by 3D printing were investigated with regard to the resulting part quality using machine learning.
- Project management
Prof. Dr. Ricardo Büttner, Business Informatics
- Project partner
Prof. Dr. Manfred Rössle, Business Informatics
Prof. Dr. Andreas Heinrich, Zentrum für Optische Technologien
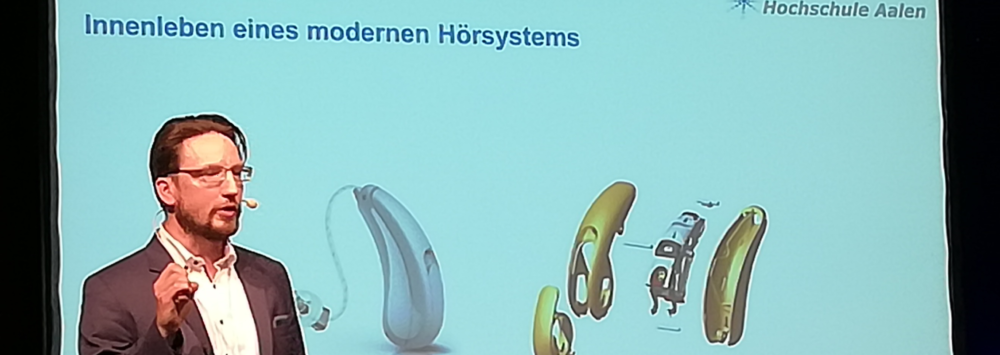
3DPräkomMed // 3D printing for high-precision components and medical device technology: new application areas through smart materials and intelligent design
01.05.2019 to 30.04.2020
Additive manufacturing for the production of complexly shaped and individualized components will enable completely new products with optimized physical properties in many areas in the future. In the 3DPräkomMed project, two subprojects investigated the use of thermostable alloys on the one hand and developed otoplastics whose hearing protection function can be functionally enhanced by an impulse sound filter on the other.
The sub-project AtheK (Additive manufacturing of thermally stressed components for high-precision applications) investigated the possible uses of specific alloys in additive manufacturing. The focus was on alloys that are thermally stable in the macroscopic range. The use of such materials is of particular importance. This is because, especially for increasingly used high-precision applications, the components must remain dimensionally stable even under usage and the resulting heating and expansion. Only materials with very low coefficients of expansion, therefore, allow the manufacture of components with a consistent fit that remains dimensionally stable at different temperatures.
In the SmartVent (3D earmold printing) subproject, additively manufactured individualized earmolds (hearing aid components) were improved in terms of their acoustic properties. Essentially, modifications were made that have a sound-filtering effect and prevent impulse-like sound from passing through the ventilation holes. The initial aim was to develop a manually-controllable filter.
- Project management
Prof. Dr. Markus Merkel, Zentrum für Virtuelle Produktentwicklung
- Project partner
Dr. Timo Bernthaler, Materials Research Institute Aalen
Prof. Dr. Steffen Kreikemeier, Health Technology
SME project
PROFM // Process-related shape accuracy of smart 3D printing materials
01.05.2019 to 30.04.2020
The application of 3D printing processes in manufacturing is a method that can be used in many fields due to its high flexibility and precision. Low volumes and high-precision product dimensions without the need for further investment are of great importance here for acceptance in companies. The advantages can only be fully exploited in the industry when it is possible to produce 3D-printed components that have the desired properties. This is currently still a major challenge in many areas.
The goal of the PROFM SME project was to produce additively manufactured components that are equivalent to conventionally manufactured products and have similar key physical properties. Since it has been shown that the use of conventionally used materials does not lead to sufficiently good results, alternative materials were tested. Specific optimization of the process parameters was of particular importance here and offers the possibility of targeted adaptation to the application in question.
- Project management
F. & G. Hachtel GmbH & Co. KG
- Project partner
Prof. Dr. Rainer Börret, Zentrum für Optische Technologien
SmartPro // FH-Impuls:
Strong universities of applied sciences - impulses for the region
With SmartPro, Aalen University of Applied Sciences has positioned itself in the top group of universities of applied sciences nationwide. SmartPro is one of ten partnerships funded through the “FH-Impuls” program of the Federal Ministry of Education and Research with around 10 million euros from 2017 until 2025. Core objectives are the sustainable expansion of the regional transfer and cooperation network as well as strengthening the research profile and innovative power. SmartPro contributes to the advancement of climate protection and digitalization, two key social challenges.